MASONRY ARCH ASSESSMENT –
Design and assessment to lift a Tunnel Boring Machine (TBM) by a mobile crane positioned on the surface of a masonry arch bridge spanning the River Thames.
Andun were contracted by BAM, Morgan Sindall, and Balfour Beatty JV as part of the Thames Tideway Tunnel project.
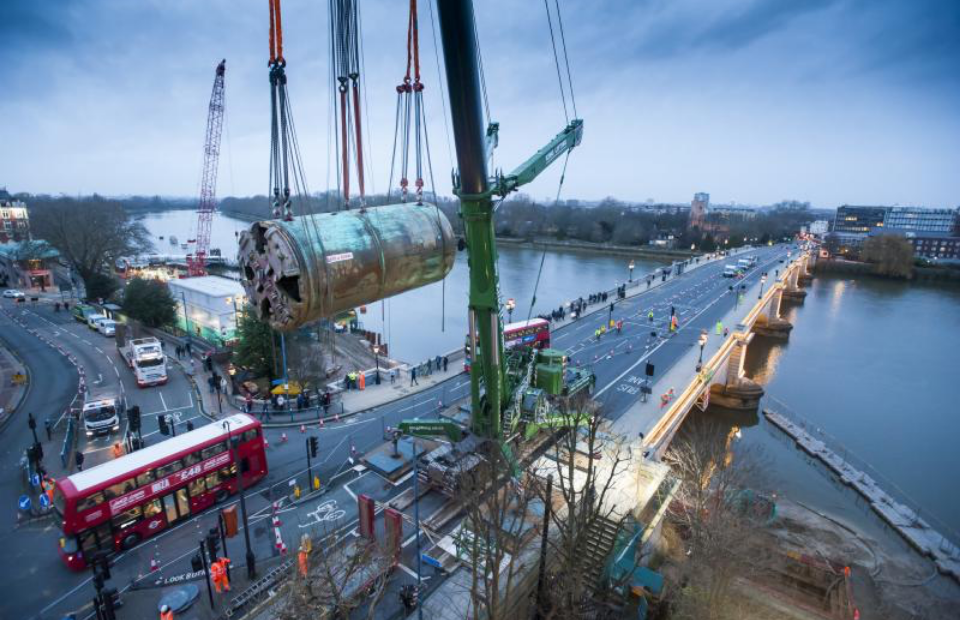
Andun were approached by the client to undertake the engineering involved with positioning a 750Te crane on the bridge and abutments of Putney Bridge. The TBM weighed in excess of 84 tonnes.
Putney Bridge was originally constructed in 1886, and the structure was widened in 1933, it was necessary to determine if the structure was sufficiently robust for the applied loadings.
The assessment included consideration of the mobile crane (an LTM1750-9.1) operating on its wheel with a gross weight of 108 tonnes and axle loads of 12 tonne, and whilst operating on it’s outriggers with a maximum outrigger load in excess of 1500kN
The requirement by local authorities that one lane of the bridge remain open during the lift for use by buses and emergency vehicles was an additional risk factor and design challenge. This required half the outriggers to sit on the pavement, which was far from ideal as live services existed beneath the footpath. These include 3 No. 24 inch cast iron water mains. A full analysis was undertaken to satisfy the asset owner that no damage would occur. A longitudinal strain analysis was carried out.
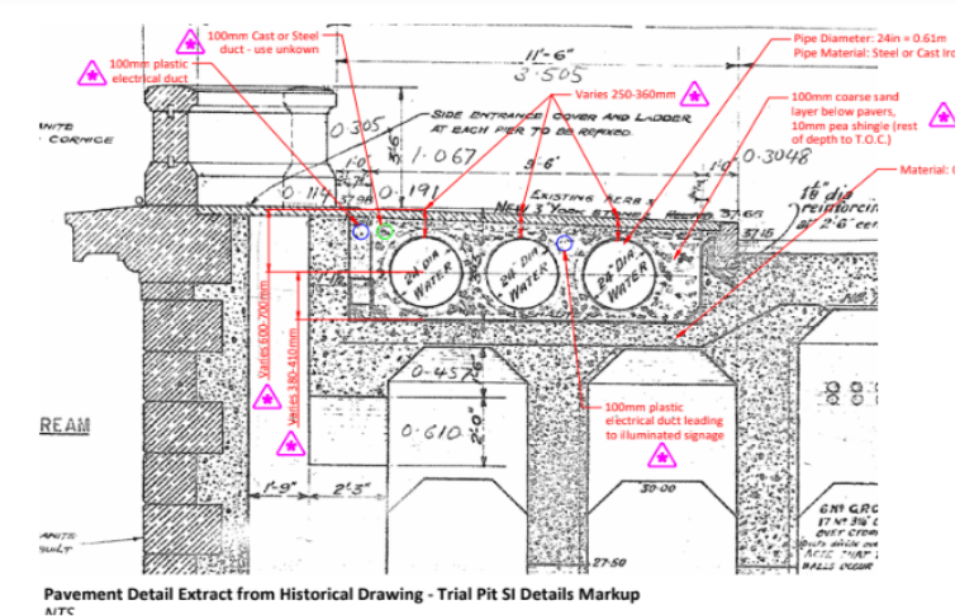
PROPOSED DESIGN CONCEPT
The crane was positioned on top of the bridge abutment with outrigger pads placed on top of navvy matts. The challenge of the pavement being at a different level to the road surface was to be solved by placing Ekki Matts on the road surface to create a level surface for the outriggers to sit on.
Assessments were also required to demonstrate the ability of the abutment to take the load and the impact of the load on the arch of the Putney Shore Span. Our analysis indicated that the increase in bearing pressure was less than 9kN/m2. This was compared to the pressure beneath the foundation that the live load the bridge was designed to carry would cause, and the difference was considered negligible.
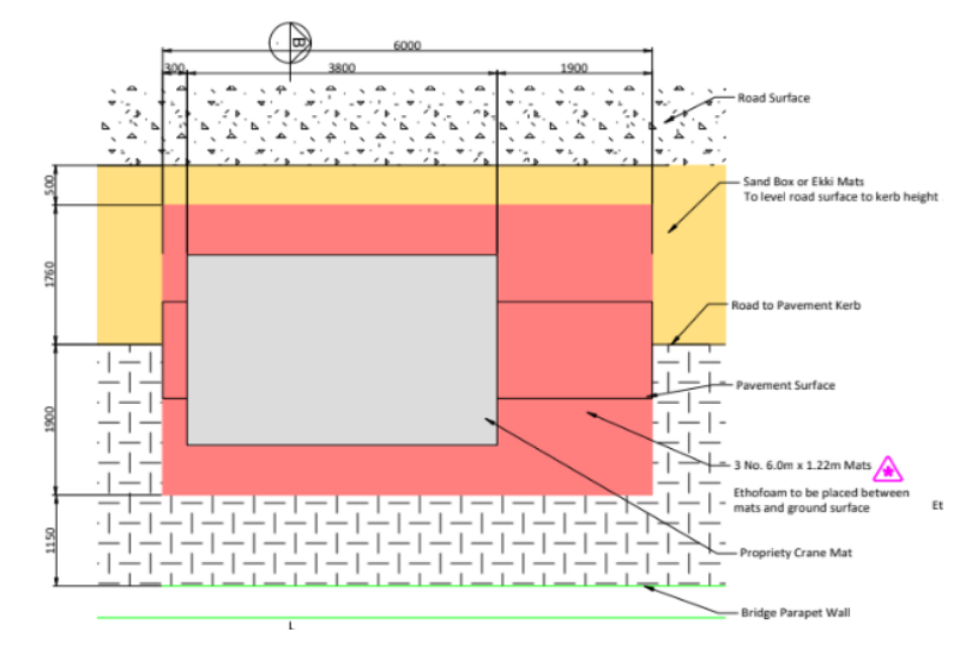
DESIGN OUTPUT:
Drawings
Approval in Principle (AIP)
DRA
Calculations.
Andun also procured the Cat 3 check directly for the project, thereby providing a turnkey solution. The cat 3 check was undertaken by Crouch Waterfall.
Following the assessment and approval by stakeholders, the tunnel boring machine was successfully lifted in February 2020.
The picture below shows the TBM being lifted with traffic on the bridge at the same time, full access to the bridge was restored as per the contractors project plan.